Materials for stickers and labels: A deep dive
Choosing your sticker or label material doesn’t have to be complicated. The most important things to keep in mind are the look you’re going for (aka which material you like best) and how durable or waterproof your material needs to be.
But there’s a lot more to know about sticker and label materials. And in this article, we’re taking a detailed deep dive!
PVC, PET, PE & BOPP films – What are they and what are they used for?
PVC stands for polyvinyl chloride. Often called vinyl, it’s popular for wrapping vehicles because of its flexibility.
Polyester (PET) is a film with excellent durability and resistance to temperature, UV, and chemicals. It’s great for labels used outdoors.
Polypropylene (BOPP) is a film with high tear resistance and rigidity, making it ideal for beverage and many other label applications. It’s the industry standard for labels.
Polyethylene Film (PE) comes in two main types: low-density (LDPE) and high-density (HDPE).
- LDPE is soft, very flexible, and has good tear and moisture resistance — great for grocery bags and food packaging.
- HDPE has strong impact strength, puncture resistance, and chemical resistance, but low gas barrier properties, making it suitable for premium label applications.
Read what stickers are made of.
Cast or calendered vinyl: what’s the difference?
The term vinyl is a common name for a print film made from PVC.
It’s widely used in the signage and custom sticker/label industry. That said, more recyclable alternatives like PP and PE are gaining popularity, especially for labels. We use a recyclable PP for our vinyl stickers and labels.
Cast and calendered refer to two different “grades” of vinyl, based on how the film is made.
Cast vinyl
Making cast vinyl starts with a formulation (aka recipe) that’s carefully mixed in a large container.
This mixture, called organosol, is then precisely cast onto a moving web called the casting sheet.
It passes through several ovens to evaporate the solvents and leave behind a solid film. The film is wound onto large rolls for further processing, usually adhesive coating.
Cast materials are very stable and can be extremely thin, which makes them highly conformable.
That’s why cast films are often used for wrapping vehicles and boats.
Calendered vinyl
Calendered films are also mixed and then kneaded in an extruder using large heated rollers to form a thin vinyl sheet.
The vinyl mixture is fed between two large counter-rotating rolls, heated to 350°F.
As it moves through the rollers, the mix is flattened by heat and pressure, forming a strip. That strip then passes through more calender rolls, getting thinner each time.
Embossing rolls add gloss or matte patterns to the film while it’s still warm. Then the film is cooled and rolled up into large master rolls.
Calendered vinyl films range from economy to high-grade.
Economy films use monomeric plasticizers to keep costs low, while higher-grade films use polymeric plasticizers for better performance.
Cast vs. calendered
Here are the key differences between cast and calendered films for easy comparison:
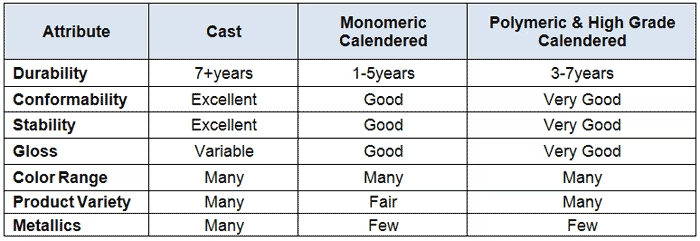
What is laminating?
Laminating is the process of applying a clear plastic film or liquid coating over a printed sticker or label.
Laminators come in all shapes and sizes. A typical wide-format roll-to-roll laminator looks like this:
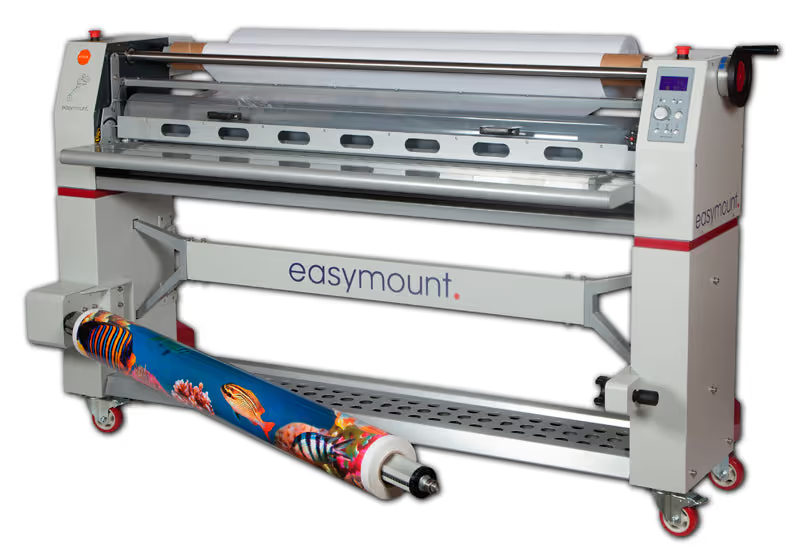
The printed roll of media (vinyl or paper) is fed through the rollers. A clear plastic film is applied on top to provide extra protection. Here’s a close-up of how that looks:
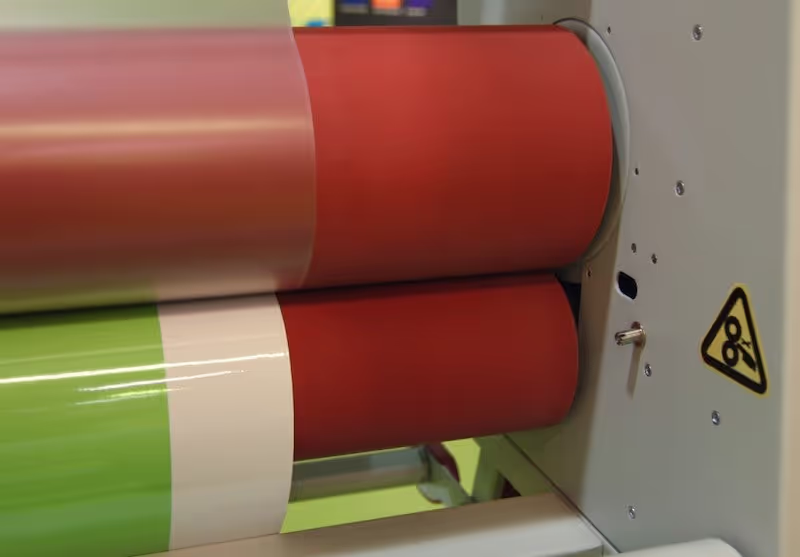
You can see the clear laminate above and the printed media coming from below. Both are fed through the rollers to apply the over-laminate.
See how can you laminate your stickers at home.
What is liquid lamination?
Liquid lamination is similar to traditional lamination, but instead of applying a plastic film, a scratch-resistant liquid is coated onto the surface of the printed material.
While it offers less protection than plastic lamination, it still provides moderate scuff resistance. It’s a cost-effective and eco-friendly option since it doesn’t use plastic.
Subscribe to our newsletter
Enter your email below to stay up to date on Sticker it's latest, including new product launches, exclusive deals and more.